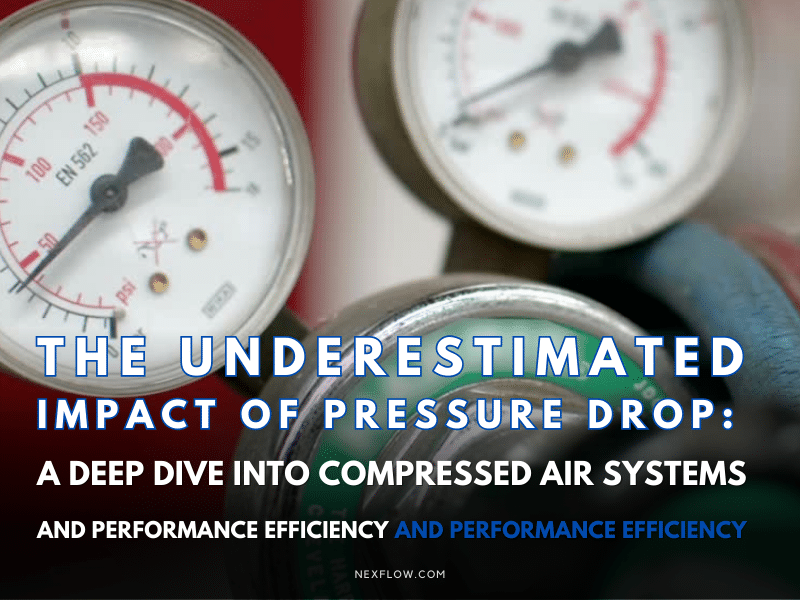
.Compressed Air Systems and Performance Efficiency
Pressure drop is a crucial aspect of compressed-air technology that is often overlooked. It is defined as the reduction in air pressure from the compressor discharge to the point of use. And is caused by resistance encountered by the compressed air as it moves through the system’s components. This includes pipes, valves, and fittings. Even a minor pressure drop can significantly reduce the system’s efficiency and operational cost. If achieving a high-performance compressed air system is the goal. Then it is essential to have a thorough understanding of pressure drop and its management.
The impact of pressure drop goes beyond technical glitches, affecting the system’s efficiency and operational costs. A higher pressure drop necessitates the compressor to work harder to maintain the required pressure. Leading to increased energy consumption and a larger carbon footprint. Additionally, a significant pressure drop can negatively impact the functioning of air-operated equipment, leading to inferior product quality and reduced productivity.
Compressed Air Systems and Performance Efficiency
Pressure drop particularly affects the performance of engineered air nozzles and air knives used for blow off and cleaning applications. Pressure drop particularly affects them.
These specialized tools require a steady, precise pressure to operate optimally. A pressure drop can lead to inadequate performance, resulting in less effective blow off, cleaning, or cooling applications. For instance, an air knife used to strip away excess liquid or debris may fall short, leaving residues that could compromise the quality of the final product or the efficiency of subsequent processes.
Prevention and consistent monitoring are the two-pronged approach to addressing pressure drop. Prevention involves designing a system that minimizes resistance by employing larger diameter pipes, minimizing bends in the piping, and opting for low-resistance components. Regular maintenance to eliminate leaks and blockages further reduces pressure drop and prolongs the system’s lifespan. Monitoring via pressure gauges, flow meters, and real-time monitoring equipment can unveil and help rectify pressure drop issues, ensuring the engineered air nozzles and air knives perform as intended.
In conclusion, pressure drop in compressed air systems is a critical factor that warrants meticulous attention. By understanding its implications and adopting a vigilant approach towards prevention and monitoring, operators can significantly improve the efficiency and reliability of compressed air systems. Timely addressing of pressure drop issues translates to energy savings and a more sustainable and productive operational environment, ensuring that engineered air nozzles and air knives function optimally to uphold the highest standards of quality and efficiency.