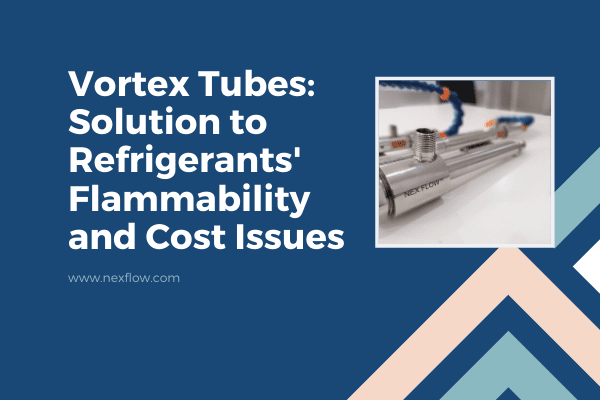
A solution to Refrigerants’ Flammability
Air conditioners are everywhere, in homes, cars, office buildings, and even factories. They are also used to cool small enclosures, in particular electrical and electronic control panels. It is these small enclosures that this article will focus upon. Air conditioners utilizes refrigerant. The original refrigerants were CFC’s or Chlorofluorocarbons which are highly stable compounds that were also used as propellants in spray cans and in refrigeration and air conditioning units. Unfortunately, due to that stability they were found to deplete the ozone layer and were replaced by hydrochlorofluorocarbons (HCFCs). HCFCs and hydrofluorocarbons (HFCs) that came right after were created as substitutes for CFCs for use in refrigeration and a wide variety of manufacturing processes due to the lower effect on the ozone layer. HFCs have little effect on ozone but contribute to global warming. All of these classes of compounds either destroy the stratospheric ozone essential to life or contribute to global warming, international agreements have been signed to eliminate their production and use by the year 2040.
One of the problems with the new refrigerants is that most are flammable. For example, Flammable refrigerants are illegal to use in an automotive air conditioning systems. There are some exceptions, such as the new R1234yf refrigerant, which is mildly flammable but only under certain conditions. Before we focus on air conditioning of electrical and electronic control panels, let’s look at a major small enclosure use and that is in automobiles. Many automobile manufacturers have approved the product. However, it is notable that initially Daimler, the parent company of Mercedes-Benz originally did not approve the use of the refrigerant especially when a video that was made public of a test showed the interior of a Mercedes hatchback catching fire after R1234yf refrigerant leaked during a company test.
Credit Wikipedia : https://en.wikipedia.org/wiki/Side_collision#/media/File:Ford_Focus_versus_Ford_Explorer_crash_test_IIHS.jpg
A thought to keep in mind is what happens if your vehicle is involved in an accident. The A/C condenser sits right in front of the radiator and contains high pressure refrigerant vapor and liquid. If the condenser is ruptured in a frontal collision (which it often is), high pressure flammable vapor will be released, almost guaranteeing an underhood fire! So presumably re-designs have been implemented to minimize any possibility of a fire in case of an accident. One possible solution to the flammability issue HFC-152a (or other flammable refrigerants) is to add a leak sensor inside the vehicle that warns the passengers if a leak occurs, and automatically opens the power windows to vent the vapors (thus, reducing the fire/explosion risk). Another solution is to redesign the A/C system so that it uses a “secondary loop” to keep the flammable refrigerant in the engine compartment and out of the passenger compartment. With this approach, the refrigerant circulates through an intermediate heat exchanger and chills a liquid (probably a water/antifreeze mixture) that then flows through the HVAC unit inside the vehicle. A recent report from the U.S. EPA says this approach meets its safety criteria, while also being energy efficient. But it does not reduce the risk of fire in a frontal collision, and it still poses a risk to technicians and do-it-yourselfers while recharging or servicing the A/C system.
Honeywell developed in mid-2018 a product called Solstice N41 (provisional R-466A), a non-flammable and lower global-warming-potential (GWP) refrigerant for use in stationary air conditioning systems. Once on the market, Solstice N41 will be the lowest GWP, non-flammable, R-410A replacement refrigerant available worldwide. This is significant and would certainly address the flammability issue. But it still has global warming concerns albeit much less. Daimler and others such as Volkswagen also have opted to use CO2 as a refrigerant instead but CO2 requires high pressure systems and of course, CO2 is a greenhouse gas. But these alternatives do deal with the flammability issues.
After all this, there is a second problem with the new refrigerants – cost. The cost of the refrigerant itself is multiple times the cost of the old ones being replaced – as much or by a factor of ten times. Then there is a cost of material changes and some redesign of the air conditioners themselves.
Now, let’s change the environment to that of a factory floor in a production setting where air conditioners or cabinet coolers or panel coolers are used to cool electrical and electronic control cabinets. The first question is whether it is safe to have a flammable refrigerant used in a device that will be mounted to an electrical device? Design has to assure that a spark from a faulty control does not cause a fire from potentially leaking refrigerant. The second is cost, due to the high cost of these new refrigerants. Replacing refrigerant could be far more common on a plant floor compared to an automobile due to heavier use and also from vibration that the air conditioner may be subjected to. If the non-flammable refrigerant is used, or if a CO2 system is used, the cost is still much higher than traditional systems used in the past and cooling systems more complex.
What is certain, is the rising cost of traditional air conditioning systems. An alternative has existed for years and that is vortex tube cooling systems. These systems like the Nex Flow Panel Cooler use only compressed air to operate, with no carbon footprint, no flammability concerns, no chemicals to replace and virtually zero maintenance. Their use does require the facility to have compressed air but this is available in most large manufacturing plants. They are used mostly for control panel air conditioning in harsh environments where maintenance costs even on traditional air conditions offsetting the maintenance costs. With the new refrigerants coming into play, and with their extra costs for refrigerants, and most costly air conditioning assemblies, the very simple design of the vortex tube operated air conditioners become more economical. In addition new vortex tube panel cooler designs are being developed to improve their efficiency and more efficient air compressors are also being offered. So while at the traditional air conditioning end capital costs go up, the operating costs of vortex tube operated systems is trending downward.
Developments in new refrigerants should be carefully watched as it affects all of us concerning the environment and its impact of manufacturing operations and all other areas where they are used. But at least for manufacturing, there is a potentially better alternative with vortex tube operated systems like the Nex Flow Panel Cooler.