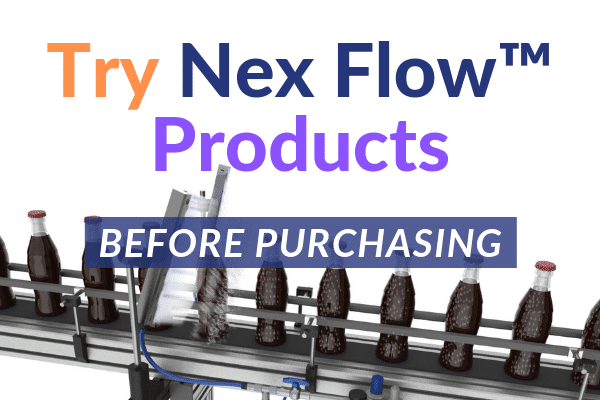
TRY NEX FLOW PRODUCTS BEFORE PURCHASING
Nex Flow offers in the USA and Canada (as do many of our representatives worldwide), a risk free product trial to potential customers and it is done in such a way to benefit all sides. Usually the trial period is limited to a maximum 30 days but in some cases, especially for larger projects, that time can be extended. Pneumatics is not a technology that is easily understood by everyone. Even in engineering schools, a great deal of teaching time is focused on hydraulics but very little in pneumatics.
If and when someone enters the pneumatic field – the focus is often in a very narrow area. Air compressor companies may give lip service to an entire system but their focus is primarily on the compressor room. A piping supplier would be focused on the piping and filtration companies would obviously be focused on the filters. Tooling, blow off, cooling and other end use application, the focus is too much on the use of the equipment without considering the entire system. That being said – it takes a great deal of experience, and deliberate interest in the entire system to truly give the best outcome to a customer. For this reason, Nex Flow insists upon understanding the entire system and the issue faced by clients before making recommendation on what to try.
A good volume of customers are in the same position as someone freshly entering the pneumatics field, and except for some basics understanding from classes and workshops, a more in-depth explanation will often help with decision making. A partial understanding of the concept can sometimes lead to inappropriate installation and test. For example, if an air knife is installed and does not work, did the issue steam from the application or installation?
A real example occurred years ago at one facility where a 24” air knife was installed for a blow off application. The issue was that the unit was not powerful enough. What happened was that the person in charge had hooked up a very small diameter airline that was also quite long. This caused excessive pressure drop in the airline so the actual pressure at the point of use was much lower and hence less powerful. At first – the installer refused that the airline might be too small – but once he accepted to change the airline diameter to a much larger one – everything was resolved.
Some companies supplying similar technology as Nex Flow® have their “application engineers” that is not always very knowledgeable about the whole system offer a 30 day unconditional trial period. With this many returns happen because no one is really there to assist when there are issues. One of our current customer had such an experience with a competitor – so much that he was skeptical about whether the system can even work for the application. The competitor sent one unit for test – it didn’t work, so the unit was sent back. With Nex Flow – we help customers explore and learn about the actual system and pinpoint why it did not work. The issue was simple – the unit was simply hooked up without the appropriate parameters. Now – this customer is using our air knives and are quite happy.
So this is why Nex Flow personnel always probe deeper to not only understand the customer’s application but the customer’s environment, and system. Is there adequate compressed air? What about cleanliness in the airline? We even ask if the compressor is far or near the application (and yes, that can make a difference in some cases). If an application is tried and does not work – we endeavor to understand why because we want to learn and improve too! Nothing is sent for trial unless we are quite sure it will work. Of course sometimes we get the opportunity to explore a new applications where we sometimes cannot guarantee if the system will work but we will still try the test if the customer is willing.
The point of all this is simple – we recognize the value of both the customer’s time and ours. It is to the benefit of both parties to understand the customer’s operation, and for the customer to understand both the potential and limits of Nex Flow® technology and the parameters of operation.
In some cases it may take time for us to review provided information and may need to inquire additional information. For customers who have already had experience using the technology. What’s very nice is that the client’s have tried and loved the product due to the high quality of manufacturer and the “extra” we provide in each product. For example, most air knife providers do not anodize their aluminum versions – we do. Our cabinet enclosure coolers are all stainless and even less costly than aluminum versions provided by old competitors. We enjoy product comparisons and as our team of researchers and engineers constantly strive to improve our products.
If you are not familiar with Nex Flow technology, or maybe you have used competitive products, successfully or non-successfully but not familiar with the Nex Flow® brand- we certainly encourage to try before you buy!