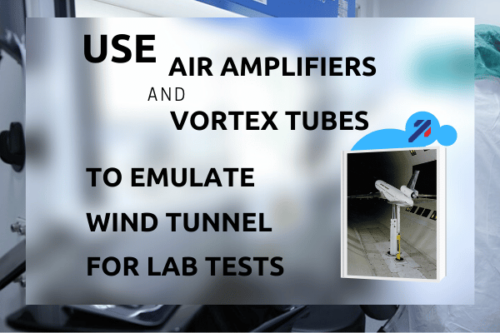
Wind tunnels are large tubes with air moving inside. These tunnels are used to test models of aircraft or other flying objects on their actions in flight. These models are scaled down versions of actual objects that will be built. Researchers and institutions around the world like NASA, uses wind tunnels to learn more about how an aircraft and spacecraft will fly. But it is not just flying machines that are tested. These Wind chambers are also used to test how an automobile shape, or windshield design will behave in environments with strong winds. Aerodynamics is the study of the flow of air or gases around an object in motion. Essentially these tunnels are hollow tubes with controllable fans at one end to test objects aerodynamics ensuring safety and performance of machines.
Airplane builders use NASA wind tunnels to test new airplane designs.
Credits: NASA
Frank H. Wenham (1824-1908), along with his colleague John Browning, invented the wind tunnel and built the first one in 1871. He described it as “a trunk 12 feet long and 18 inches square, to direct the current horizontally, and in parallel course.” As a British marine engineer he studied the problems of human flight and had many publications. He also made a huge influence in the development of aeronautics. Their experiments showed that high aspect ratio wings – long and narrow—had a better lift-to-drag ratio than short stubby wings with the same lifting area. Wenham may have been the first scientist to use/coined the word “aeroplane”. Aviation writer Carroll Gray says Wenham’s work may have been an important influence to the Wright brothers.
As mentioned above, wind tunnels typically use powerful fans. But – it is possible to use Nex Flow compressed air operated Air Amplifiers instead of fans for a miniature wind tunnel. To get the system to work, the gap setting on the Air Amplifiers will have to be increased to approach the power needed for testing even a very small object. Although there are limitations to using compressed air for wind tunnel emulation – they do offer some advantages like having a lower noise level and their ability to be combined with vortex tube technology for testing at sub-zero temperatures.
Powerful fans overcome back pressure created by the length and overall volume in the tunnel. Compressed air amplifiers however cannot be “revved up” like a motor and are subject to this back pressure limiting the length and volume of a tunnel where it can be used. However for very light and small objects, it is conceivable to use an Air Amplifier to operate a miniature wind tunnel.
Air Amplifiers take compressed air that is consumed and converts the pressure normally lost as pressure drop and noise into high velocity and high laminar flow. With fans you can control this velocity and flow by making the fan turn faster or slower. With Air Amplifiers you have some limited control with input pressure but in a much more narrow range which should suffice for a small miniature tunnel. A common setup at exhibitions is to attach an Air Amplifier to a stand and have the amplified airflow support a beach ball which can be held a few feet above the vertically aimed Amplifier. The object tested in an Air Amplifier operated miniature wind tunnel would have to be in the low weight range of a beach ball to be useful. A powerful compressed air operated engineered nozzle, or a series of engineered air nozzles might be paced at one end of a miniature wind tunnel for more force. After a short distance, the combined airflow could produce enough velocity and flow to be useful for testing small, light objects. One advantage of both using compressed air amplifiers or laminar nozzle is the lower noise level than you would get from a powerful fan.
Vortex tube technology however, does offer one advantage for a special type of wind tunnel. A vortex tube is a device which takes compressed air and divides it up into a hot and cold stream. This cold stream of air flow can go to very low, sub-zero temperatures. Vortex tube commercially are available in air consumption ranges of 2 to 150 SCFM. However, there is no reason that a vortex tube cannot be made much larger to consume several thousand SCFM. In some research applications for wind tunnels it is necessary to study aerodynamics at sub-zero temperatures (i.e. the behavior of military aircraft in arctic or subarctic conditions). A much larger vortex tube consuming one thousand SCFM or even more can produce very cold temperatures of -40 ˚C and even colder if the compressed air supply is cooled further. While it would seem to be uneconomical to use such high volumes of compressed air, that high energy cost is offset by the fact that you do not have to cool the air to the sub-zero temperatures required for testing. Also, the efficiency in the production of the cold temperature actually goes up as you increase the size of the vortex tube. Let’s presume you have 10,000 SCFM of compressed air supply. With vortex tubes the temperature drop increases (you get colder temperatures) the more air you exhaust at the “hot end”. So if only 30% (3000 SCFM) goes out the cold end to get that -40 degrees Celsius. The cost of cooing 3000 SCFM of a fan produced air flow to that cold temperature using a more traditional means of cooling will be very high. You also will be using refrigerant which will be costly, and need maintenance. In using a special vortex tube you only have the compressors and the wind tunnel taking the flow, at the low temperatures you want. This minimizes any maintenance involved. It is actually a very simple system.
So while there are certainly not a great deal of applications where a wind tunnel is needed that produces such low sub-zero temperature airflow, there are certainly enough when dealing with some military and space equipment applications where aerodynamic tests results under extremely low temperatures are required. In this case, using a special large vortex tube is a possibility. Such special wind tunnel has been built in the past with very large vortex tube design.
For unique applications such as the above – Nex Flow has experience in special vortex tube design. Some years ago a two meter long vortex tube was developed for an application (not a wind tunnel however) which used natural gas as the medium instead of compressed air. The parameters of the application had to be addressed to develop the optimum design and the supply gas was at very high pressure. The application remains proprietary but it does indicate that vortex tube technology can be adapted and made effective and economical for special applications where cold temperatures or overall cooling is necessary and where using traditional cooling would not be as effective or economical.
So for wind tunnel applications, Air Amplifiers (and even Engineered Air Nozzles or jets) can apply to miniature wind tunnel for small and lightweight objects. If the wind tunnel requires sub-zero temperatures, vortex tube can be integrated as part of the system. Do note that as these are two different things entirely, you connect a vortex tube to an air amplifier