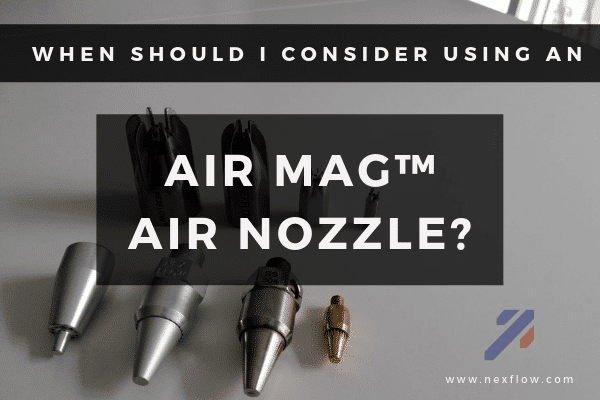
Compressed air nozzle – air saving nozzle or engineered blow off nozzles are good to have but there are so many of them. This is why many people get confused and stick to the same products they are familiar with even if there are more efficient versions out there. Worse yet, in some cases engineered nozzles are not used at all and open pipes and tube are used. The price range for nozzles also vary tremendously in the market. The problem stems from a lack of compressed air knowledge to make a proper decision.
In a recent Compressed Air Best practices article, there was an example of a company that reduced compressed air cost by over half – the biggest saving was actually in replacing compressed air jets and pipes with proper engineered nozzles. This alone indicates the tremendous importance to keep compressed air costs low. Another reason to choose a well designed nozzle is noise level. The exhaust noise from compressed air from open pipe is very loud – not only uncomfortable but also very dangerous to personnel. A well designed unit can reduce this noise and meet the OSHA standards for safety (dead end pressure must be less than 30 PSIG). You get energy reduction, noise reduction and safety.
But how do you choose the best compressed air nozzle? Do you choose the cheapest? The most expensive? So many designs do look the same, at least on the outside. But, the fact is, they are NOT all the same – even if they have the same external appearance. Here is why…..
First of all there are two basic designs available – the cone shaped air nozzle which is the oldest design and a bullet shaped design that was first invented in 1989 so it is relatively new. Both designs save energy, are safe and reduce noise levels. The bullet designs focus on noise reduction but also energy reduction and high force. In comparing the two designs the main difference are as follows…
On one hand, the Bullet nozzles gives a higher force/unit air consumption.
On the other hand, the Cone nozzles produce a higher flow output /unit air consumption.
This would imply that for applications where force is more important such as in part ejection the tendency would be toward choosing the bullet design. As for cooling, the flow output is more important and the cone shaped designs would be the wiser choice. Bullet shaped nozzles are more expensive to manufacturer and as a result are more costly to purchase.
Having said that, in either design, the performance can still vary quite dramatically. For example, we have one customer who tested a wide range of cone nozzles as for the particular application the main criteria was mass flow and not force. In this case both efficiency and noise were still important as was cost since the customer is an OEM and purchases a large volume. The Nex Flow® unit was the most quiet and the most efficient in both output and energy use. This was despite the fact that all the nozzles tested looked quite similar emphasizing the fact that “it’s not just the outside, but it’s the inside that matters”.
The same applies to the bullet nozzles. There are endless copies on the market, many claiming performance to be the same or nearly the same as the item(s) they copied. When Nex Flow® decided to create the Air Mag® nozzles a decision was made to make sure they produced the highest force/unit air consumption (SCFM) against all other brands on the market. So at least at this point in time, our Air Mag® nozzle is the most efficient bullet shaped design in the market. The other goal was to price the units lower than competitive unit with the near, or close performance as the Nex Flow® designs. Noise levels also had to match or be quieter than other models of the same size. These goal were all achieved giving birth to the first Air Mag® Air Nozzle of the series (Model 47004AMF). Price and noise level is important and an immediate means for customers to evaluate the quality. Exceeding or at least matching the performance of any competitive nozzle is important in order to easily replace less performing and/or inefficient nozzles and improve upon the application or match the previous application.
This is because “differences” are far more visible to pressure drop than other products such as air knives and amplifiers when one is replaced with another. If a competitive unit uses even as little as one additional SCFM to produce the same force, that extra flow can affect the actual pressure entering the nozzle reducing the force and not working as well. We know of one specific instance where a competitor tried to replace one brand with another that was lower in price. While similar in design, the performance did not match up despite claims of equal force in their literature. What was ignored was the air consumption so the replacement did not work. The Nex Flow® Air Mag® nozzles however would work because of its improved efficiency. This rather sensitive reaction of nozzles to installations from pressure drop tends to be the reason why companies usually opt to stay with the same brand once a decision on the product is made as maintaining consistency in output is important in production. The Nex Flow® approach allows for customers to easily test and be rest assured that they can replace possibly more costly brands with the lower cost Nex Flow® nozzle with no risk to the production operation.
Additional advantages in the Air Mag® design is more rugged for greater safety and longer life, patented hole design to improve efficiency as well as a sleek body design to keep exhaust noise levels low and allow for the unit to work effectively at a greater distance than other products on the market. This extra distance can be very important in applications where the nozzle cannot be placed close to a part.
Efficiency in force per unit of air consumption, rugged design, longer distance for effective operation, right pricing, low noise levels and safety are all good reasons to consider the Nex Flow® Air Mag® Air Nozzle.