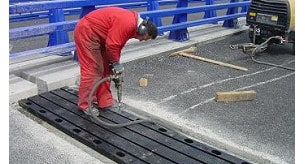
WHEN USING COMPRESSED AIR
While it is known that compressed air is costly to use, there are still things that happen on the shop floor that creates a great deal of waste. The key to maximum efficiency in the use of your compressed air supply is in the delivery and end use of your entire pneumatic system. Ways to maximize the use are as follows:
1. Check for leaks. 30% of energy loss is typically lost in air leaks. These are often ignored since, unlike liquid, air leaks do not make a mess. But they drain dollars. You can use the “soap and water” technique on fittings to check for leaks, or hand held leak detectors to find them and repair. And easy way to check if your system has major leaks is simply charge up your system, turn the compressor off, and see how fast the pressure downstream goes down. If it stays charged – no leaks.
2. Upsize your air hose. All air hose will have some pressure loss. Companies seem to have a great deal of small 8 mm tubing or ¼” hose around which is easy to move around but creates much more losses than larger tubing or hose. Obviously you need to check against the air consumption at the end, but if possible use a larger tube – 12 mm instead of 8 and larger hose, 3/8” instead of 1/4” and even larger if the demand side uses a lot of air. There are charts easily available on line that gives you the pressure loss is different sizes of hose and tubing to determine the best size.
3. Minimize the length. As with smaller diameter of tubing or hose, so will the greater the length increase pressure loss. So keep lengths as short as possible. If you have to go longer – use a larger diameter.
4. Lubricate tools. Use the proper type for each tool that promotes long life to the particular tool and does not damage parts like O-rings and other internal parts. A good in-line system should keep them working properly.
5. Do not lubricate blow off. When the air is used for blow off or cooling applications do not lubricate as this will only block the particular nozzle used. If the entire airline is well lubricated, use an oil removal filter upstream.
6. Use safety blow off nozzles. There are engineered nozzles, air amplifiers, and air knives on the market for blow off that will reduce the compressed air utilized as well as (most) meet OSHA standards for dead end pressure for safe operation and also to keep exhaust noise levels low.
Awareness of the above can go a long way towards saving energy, extending equipment life and providing a safe environment is the use of compressed air.