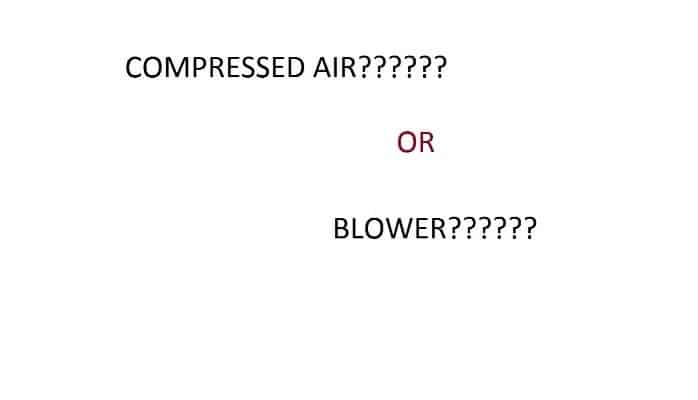
Both low pressure blowers and high pressure compressed air is used for blow-off and cooling applications. Much has been made of the higher energy cost in using compressed air over the last 15 to 20 years which all started when the cost of compressed air “leaks” came to light, putting added focus on compressed air cost. However, the choice between the two is not always so clear as there is far more than energy cost to consider.
1. Blowers have high purchase price which needs to be considered if a compressor already exists.
2. Blowers take up space and must be close to the application – so if space is an issue the compressed air option may be better
3. Unless a very high powered blower it will not dry nor cool as well as a compressed air blow off. Many times a blower is installed and then supplemented with compressed air simply because it does not dry or cool adequately cutting into perceived energy savings. Blowers rarely have the same blow off power of a compressed air blow off. Most likely you only need to use the compressed air blow off at lower pressure than line pressure. You can reduce the energy use of compressed air by over 60% if you use only need 30 psig for the application as an example. In addition, blowers cannot be cycled on and off. If the need for blow off is intermittent, the larger the gap between the time the compressed air blow off needs to work, to when it can be cycled off, it approaches the same level of energy use, and in some cases even less.
4. Blowers are noisy – a major safety issue that often exceed OSHA exposure levels which compressed air products to reduce noise for blow-of and cooling exist
5. Blowers have higher maintenance – filters changed every 1 to 3 months, belts replaced every 3 to 6 months, bearing replacements
6. Difficult environments affect choice. When environments are too cold, too humid or too hot, blower maintenance goes up to the extent it can me more than the energy cost of using compressed air.
Questions to ask yourself when considering which technology to use
Actual force needed for cooling or blow Compressed air blow off companies often minimize the energy cost they need and maximize the maintenance and capital costs of blowers unrealistically. Blower companies do the reverse – the stretch the energy cost used in compressed air by calculating costs at higher pressure than may be needed, not factoring in intermittent use, and minimizing the maintenance costs that may be incurred in using a blower. They also rarely mention the noise factor which is a major safety issue an the extra space the system can take up. In making the appropriate choice you need to ask the following:
1. Get an true Idea of maintenance cost on the blowers, repairs, replacement parts, and downtime cost of maintenance for the environment that it would be in. The more harsh the environment, the more it favors compressed air. If less harsh a blower.
2. Is noise an issue? If so, the compressed air is favored.
3. What is are you drying or cooling? How much force is really needed to do the job? Is the part(s) continuous or intermittent (which would allow cycling on-off if compressed air is used). If continuous, it favors a blower an if intermittent, it favors compressed air.
4. Do they have excess compressed air capacity? Obviously to use compressed air you would need to have the capacity.
As energy costs go down with green source coming into play, and maintenance costs rise due to lack of qualified personnel, and as factory noise issues take precedent, these factors will also have an influence into the proper choice to make favoring compressed air over the longer term.