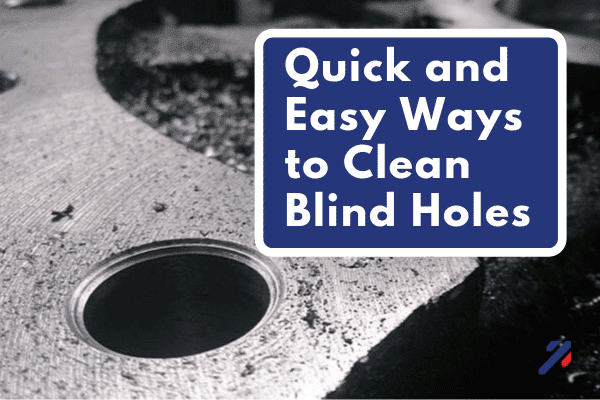
A blind hole is a hole drilled into a part. A blind hole refers to a hole that is reamed, drilled, or milled to a specified depth without breaking through to the other side of the workpiece. The etymology is that it is not possible to see through a blind hole. In this instance blind may also refer to any feature that is taken to a specific depth. More specifically referring to internally threaded holes (tapped holes). Where cleaning is automated safety is not a big issue because personnel are far from the cleaning zone. But, for manual cleaning, safety is a serious concern that must be considered and addressed.
After a hole is drilled – normally it must be cleaned of dirt and debris. Because a blind hole does not completely pierce through, it is often much more complicated to clean. In order to effectively clean inside the confined space of a blind hole there must be a means to introduce and remove air and or liquid from that confined space. For an “exchange” to take place, one media must be entering the blind hole through the single available access simultaneously as the trapped material exits through the same access. Buoyancy, fluid dynamics and surface tension all come into play. If using a liquid to clean a blind hole some issues must be considered. In most cases, blind holes are first filled with air as they enter the cleaning process. The initial challenge is to remove the air from within the blind hole and replace it with the liquid as the first step in cleaning. If the open end of the blind hole is facing down, the buoyancy of the air will prevent its escape from the hole much like an inverted drinking glass or a diving bell.
If the opening of the blind hole is up, it allows the buoyancy of the air to cause it to exit the hole depending on the cross section of the hole. This is not a problem with holes that are, for example, 1 square inch in cross section, but as the size of the hole becomes smaller, forces of surface tension can prevent the liquid from giving way to the passage of the trapped air.
So for very small, deep holes using compressed air in many cases can be a better alternative. This is where often air guns with small nozzles are used to blow into the hole and clean out the dirt. In either using air only, or using liquid, the person doing the cleaning has to wear protective clothing and eye/face and body protection because debris may be flying out of the hole as it is cleaned. For this reason some alternative cleaning systems involving air guns have been made.
One common one that has been copied is to use something similar to the Nex Flow X-Stream Hand Vac. The unit is set in vacuum mode. At the outlet end of the unit a plastic piece is attached. A small tube is inserted into the plastic piece and connected to the opposite end of the air gun which has the air blowing. Therefore the small tube at the vacuum end is blowing air from this tube at the same time the gun is vacuuming. The theory behind this setup is that the small tube blows air into the blind hole and the debris blown out of the blind hole flies up and is vacuumed away by the gun into a collection bag connected to the air gun. The plastic attachment covers the entire opening of the blind hole so that the dirt and debris do not fly onto the person holding the cleaning system enhancing safety.
In real life however it is not a very good system. First of all, the tube cannot blow very far into the blind hole because it loses force quickly the deeper the hole is. Second, the vacuum effect works against the force coming from the small tube. The air resistance weakens the cleaning effect. In turn this also weakens the vacuum effect. So although it is a nice idea….it is not the best way to clean blind holes.
Nex Flow had considered such a system in the past as well since it is easy to convert the Hand Vac to do this. But we did not want to sell an inferior product. Hence the development of the Nex Flow Blind Hole Cleaning System. It can clean all kinds of drilled holes to a depth of up to 525 mm or 20 inches and holes up to a maximum size of 1 inch or 25 mm. The first requirement was to come up with a series of various small diameter extension tubes to be attached to an air gun that would carry compressed air down inside the blind hole. The exit of the air gun has a rubber attachment that goes over the air tube extensions and which covers the blind hole. There are three different sizes of these “adaptors” each to handle a maximum diameter of hole of either 16 mm, 20 mm, and 25 mm. The adaptor covers the entirety of the hole to protect the user. Being made of rubber it provides a much better protection than plastic. The various lengths of tube attached to the air gun are for various depth ranges of the blind hole. They are interchangeable as are the adaptors. There is no vacuum required. By inserting the appropriately sized length of tube that delivers the compressed air, the force from the air is more than enough to force the dirt and debris back up and out of the blind hole, thru the air gun and into an attached collection bag.
This system is far superior than the previously described method and actually uses much less compressed air to complete the task. It has proven to be far more reliable, safe, rugged and efficient as well as much easier to use and with greater flexibility. The only drawback is that the diameter of the blind hole is limited by the diameter of the tube extension as you require space around the tube to have the material blown out. However, for some shallow depth and very small diameter bind holes Nex Flow has provided some system where a small tube is used that is just outside the blind hole but covered by the adaptors to clean the parts. But for most applications, even for deep blind holes, it is a cost effective solution for cleaning.