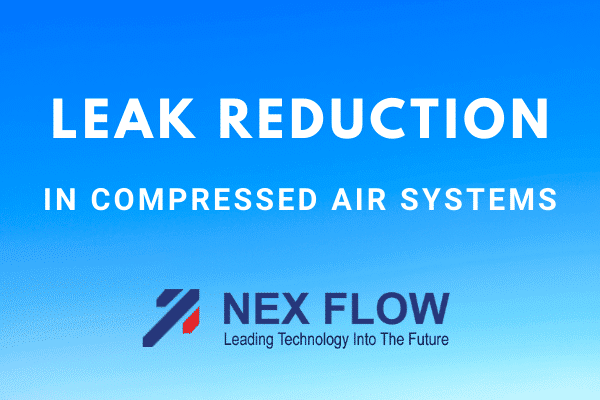
With the tightening of labor availability and the increased mandatory safety measures an often neglected area in compressed air systems is to check for leaks.
Compressed air auditors rightfully focus on improving air compressor efficiency usage and on leaks.
The importance of identifying leaks remains strong to minimize energy waste. The following was posted in 2017 but is still applicable today although more sophisticated systems are now available to detect and even monetize leakage costs as well as increased use of flow metering devices to not only improve efficient use of compressed air, but can also indicate possible leaks.
The average leakage rate in a compressed air systems can be as high as 30%. Leaks in a compressed air system do not always get the attention they deserve because you are leaking an odorless invisible gas that does not represent a direct hazard. Certainly not like a very visible water leak. The increasing volumetric flow rate caused by air leaks gives rise to higher energy costs for generating compressed air.
Even a small leakage with a diameter of only 5 mm (or the total diameter of the whole of many small leaks adding up to 5 mm) in a 100 PSI compressed air network has high cost, i.e. air losses of 65 SCFM. At 2000 hours a year and a conservative cost figure of 25 cents/1000 cubic feet that amounts to almost $2000.00 a year.
There are various ways of establishing or measuring the quantity leaking out:
1. Establish the leak by emptying the compressed air receiver: This involves measuring, for example, the period during which the pressure drops by 15 PSIG. During measuring, the tank is no longer supplied with compressed air. Assuming that the compressed air flows out isothermally, the quantity leaking out of a compressed air system can be approximately determined by applying the following formula:
Volume of the Leak =
(Receiver capacity) X (Initial receiver pressure-Final receiver pressure)/time measured
2. Determine leaks from the compressor running time or the duty cycle of the compressor. This method can be applied to compressors with intermittent and no-load operation only. All air consuming devices need to be turned off or blocked. Owing to leaks in the system air will leak out and the network pressure has to drop. Over a measured period of time the total running time can be noted. To obtain a good representative result, the compressor period should include several switching internals of the compressor
3. Determining leakage by measuring compressed air consumption: Data loggers can calculate the compressed air consumption of a compressed air station via the load cycles of the compressor. Existing leaks can be deduced from these measurements.
Locating leaks can be done by three methods:
Soaping the compressed air connections
Noise development analysis
Ultrasonic measuring devices
It is also notable that 70% of compressed air leaks occur in the last 30% of the compressed air system.
In addition to compressed air delivery piping joints and bends, specially weak spots to check should be:
Leaking quick release couplings
2. Leaking connecting hoses to the respective compressed air consuming devices
3. The use of old, unchecked condensate drains (floating drains, time controlled solenoid valves)
4. Outdated compressed air consuming devices (e.g. Overblowing compressed air tools)
and
5. “Disintegrated” seals on pneumatic control elements