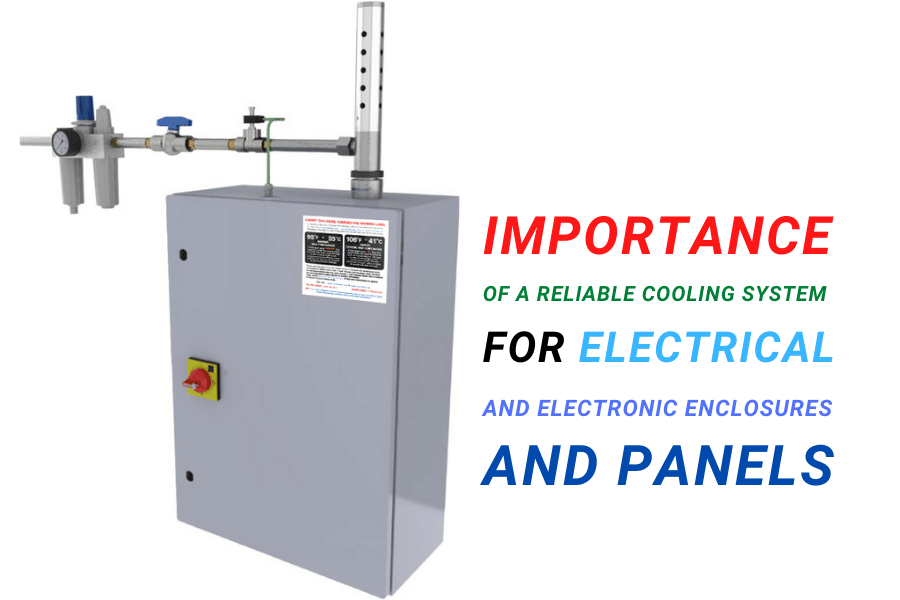
When costly electrical and electronic equipment that maintains the operation of a factory go down, production stops. Critical servers and security systems that drive production is of primary importance in a manufacturing operation not only for production but even for employee safety.
Maintaining the right temperature inside electrical and electronic cabinets require a reliable cooling system. Elevated ambient temperatures in a factory environment can cause costly system failure.
1. Reliable Cooling systems enhance the useful life of controls. When temperatures rise above maximum operating levels, electrical component life can be reduced significantly. A reliable cooling system keeps the panel temperature below the manufacturer’s recommended maximum value, something simple fans and a building’s HVAC system cannot guarantee.
2. Employee Efficiency is increased. Any company wants employee time spent on improving the business and the bottom line, and not dealing with unexpected breakdowns. While the unexpected does happen those related to control panel shutdown can be reduced dramatically with a reliable cooling system.
3. An Ideal Air Conditioning Systems is Maintenance Free or at Least Minimal. Most cooling systems require regular checks, such as filters on an air conditioned panel. If not changed regularly especially in a dirty environment one of two things can happen: if not changed a dirty filter can cause poor air circulation and overheating or, if the filter is missing, then dirt can get inside an enclosure and coat, and damage controls or at least reduce their lifetime significantly. Too often these things get missed or just ignored due to lack of maintenance time.
4. Prevention is Always Less Costly. Preventative maintenance starts with machines working in a properly controlled environment. Just as people work better in a better environment, so does equipment. Poor temperature control inside electrical and electronic enclosures is damaging both economically and from a safety perspective. The use of an efficient cooling system is both economically more profitable and much safer to personnel.
Let’s go deeper on each of these points.
Reliability is becoming more important as labor costs and even labor shortage increase over time. It is important that ANY product for cooling is reputable both in quality as well for technical support should anything actually go wrong. But it’s more than just the supplier’s reputation. Any product chosen should consider the factory environment in which it is placed. Utilizing a fan to cool the inside of a control panel in a dirty and hot and humid environment without considering the environment in which the panel exists can invite trouble. The manufacturer of the control panel does not always have control or any say in which the panel is placed. If the environment is nasty then that should have a serious impact on the cooling method chosen.
Employee basic responsibility is to keep the plant operating. This means an acceptable preventative maintenance program and not only just responding when a problem occurs. If problems persist, the more thorough investigation should be made. Too often however, the problem is not addressed and much time and cost is spent fixing things over and over. For control panels, if the panel door is consistently “left open” because it’s just too hot inside the enclosure, then it should be addressed. It is not only unsafe to leave electrified enclosures open while operating, it is also in most placed illegal. Addressing these problems expeditiously can only improve the environment overall as well as reduce downtime and other potential problems.
Labor costs are significant in any production operation and labor efficiency is important. Every time an outside service person is brought in, some employee must escort that person in the factory, perhaps spend time while that person goes thru a safety protocol training and of course, there is downtime when maintenance is done. Even if no outside person is needed for service, there is still a downtime cost when maintenance is performed by employees. If labor cost can be optimized by reasonably priced solutions that are relatively maintenance free, it should be done.
Prevention is helped by a properly maintained preventative maintenance program and can be further improved by monitoring. There has been and continued=s to be tremendous advances in monitoring of all sorts of equipment especially rotating equipment such as pumps and motors. But what about control panels? While so much is spent for monitoring other equipment the electrical and electronic enclosure should not be ignored. It is just as important in any production line since it keeps that motor or pump running!
HERE IS A NEX FLOW®SOLUTION especially ideal for hot and dirty environments:
We suggest the Nex Flow® Frigid-X® Panel Cooler
They are:
1. Reliable as they do not require electricity to function,
2. Free up Employee Time due to its reliability
3. Essentially Maintenance Free with no filters to change or worry about and even keeps control panels clean by keeping out dirty plant air, and
4. Prevents Downtime due to Overheating by maintaining the proper environment inside a control panel.
Every Panel Cooler comes with a Temperature Indicator sticker that you can put on the outside of a control panel to indicate if the approximate temperature inside the enclosure. Extra stickers can be purchased for other panels. Monitoring does not always need to have a high cost.