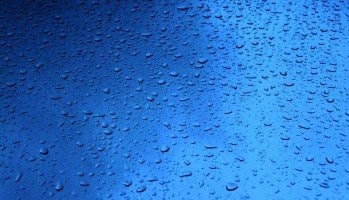
Compressed air is viewed as a costly method for blow off and cooling applications and some look to electric motor driven blowers as a replacement. This is a reasonable with a focus for energy saving being a major factor. However, the cost of changing to a blower system is NOT always the most economical solution. What should be considered are he following six (6) critical factors:
1. Will a blower system work as well as the compressed air system? You actual force and needed for the application needs to measured. This will determine what size, and even if, a blower can do the same job. If a compressed air system is replaced with a blower, and it is found to be less effective, it will slow down production and these losses will offset any energy savings. In fact, what usually happens is the blower system gets a supplemental compressed air blow off added back negating the anticipated energy savings. A car wash system can be effective with blowers because it is “slow”. But a production line with a more complex item to dry may require the power of the compressed air blow off.
2. What is the actual energy used? A company offering compressed air blow off tends to provide examples minimizing their overall cost against blower system and companies offering blower systems do the reverse – they provide examples maximizing compressed air cost against their blower systems. The answer is usually in between. In this case, the actual force needed for the application will determine what is best. For example, if the compressed air application only needs to be at 40 PSI to provide the force required, then the actual energy needed is much less than if the pressure has to be 80 PSI. In fact, it drops to about 50%! Also, compressed air systems can be cycled on and off instantly. A blower system cannot, otherwise you burn pout the motor. As a simple example, if the compressed air is only on 70% of the time, that is a reduction of 30% energy use. Both these considerations, when weighed against the use of a blower system can sometimes equate to actual energy use close to and even “less” than a blower system. Sometimes a blower system is combined with a heater which can also be a major source of energy use that needs to be considered. Like the blower itself, the heating coil is not cycled on and off, at least not quickly.
3. What about maintenance cost? As compressed air has many uses other than blow off applications, the maintenance cost will not likely change for the existing compressors. Compressed air blow off products themselves are essentially maintenance free. However, when you “add” a blower system you now have another machine to care for. This is a cost. Also, you typically do not have a central blower system – you have one per machine. That increases maintenance costs which need to be carefully evaluated. It is not uncommon to have increased maintenance costs more than offset any perceived energy savings. In a world with a shortage of qualified maintenance personnel, this is a serious consideration.
4. What about noise? Compressed air blow off technology exists to reduce exhaust noise to much lower levels than just open pipe or tubes and are increasingly utilized. But when you put in a blower, you now have to deal with increased noise – noise much louder than a compressed air blow off. This is detrimental to worker safety and can even affect labor relations if the factory environment gets “louder”.
5. What about space? Compressed air blow off products take up very little space. When you add a blower – you take of more space. This may or may not be a consideration.
6. Downtime Risk? Typically compressed air systems are off a central system and compressor, or series of compressors with backup. However, a blower would be “per machine” so if one blower goes down, that line is down. Reliability requirement should be seriously considered in the particular application.
In the real world, either system is best depending on the factors above as well as the particular goals of he company. Each system has their advantages and disadvantages but one is objectively better than the other depending on the particular application.