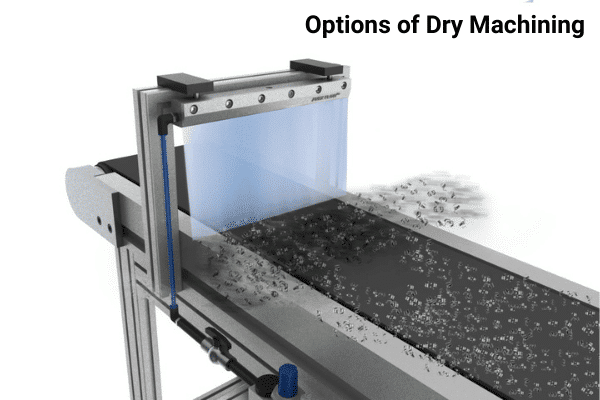
Options of Dry Machining
The positive features of metalworking fluids have long been established and include friction reduction, cooling, corrosion protection, welding protection from the tool to the workpiece and the washing away of metal chips. However reducing cutting fluid use offers the chance for considerable cost savings. Tool life may even improve. The problems to address in machining involve the following: chip removal, safety, cooling and lubrication where necessary.
Today, the economic cost of using fluid has gone way up —including their management and disposal—account for 16 percent of the cost of the average job, up from under 3% two decades ago. Because cutting tools account for only about 4 percent of the total cost of a machining project, accepting a slightly shorter tool life for the chance to eliminate the cost and headaches of maintaining cutting fluids could be the less expensive choice. And tool life may not even go
down thanks to coatings which have been developed for tooling over the years. In addition, there are safety concerns to deal with in the use of cutting fluids. OSHA established the Metalworking Fluid Standards Advisory Committee (MWFSAC) in 1997 to develop standards or guidelines related to metalworking fluids. In its final report in 1999, MWFSAC recommended that the exposure limit be 0.5 mg/m3 and that medical surveillance, exposure monitoring,
system management, workplace monitoring, and employee training are necessary to monitor worker exposure to metalworking fluids.
So there is a movement to dry machining for both economic and safety reasons. One of the biggest concerns in dry machining is the removal of chips after machining. Cutting fluid not only cools and lubricate but it also washes away chips. With dry machining, alternatives must be considered and one is the use on an integrated compressed air removal
system. These systems can minimize cost of air using air amplification technology such as Nex Flow Air Mag® Nozzles and standard Air Nozzles for chip removal. Their design allows them to remove chips eve when placed at some distance away due to their laminar air flow.
Safety is immediately improved with dry machining whenever the use of coolant and/or lubricant is eliminated or at least decreased. Advances in the types of coatings applied to cutting tools have been the major factor in improving the feasibility of dry machining to improve tool life in dry machining applications. What is left is lubrication where needed and cooling. With cooling several types of systems are being developed using cryogenics, and even heat pipes, some which involve the use of costly and environmentally unfriendly refrigerants and also costly system designs. The use of vortex tubes is for cooling is a relatively low cost viable option. Tests have shown that vortex tube based air cooling provides a highly efficient heat removal mechanism for metal cutting and delivers thermal cooling performance very much comparable to traditional liquid coolants without the inherent chemical exposure risks to machine operators and harmful impact on the environment. The tool life is very much unchanged and the surface finish quality of workpiece shows no significant change in comparison to liquid cooling. The Nex Flow Tool Cooler was developed for these applications. When lubrication is required the ideal would be to minimize the amount of lubricant needed. Using a vortex tube to cool the lubricant just before it is applied can reduce the amount of lubricant used as much as 20%. The patented Nex Flow Mist Cooler which incorporates vortex tube technology was created for these applications where some lubrication is needed.
Both the Tool Cooler and Mist Cooler are low cost alternatives to use in dry machining.
In summary….
Dry Machining Options
Cryogenics and Micro Lubrication – effective but costly designs
Heat Pipe – limited in cooling effectiveness but low cost
Tool Cooler or Mist Cooler with vortex tube – effective and low cost