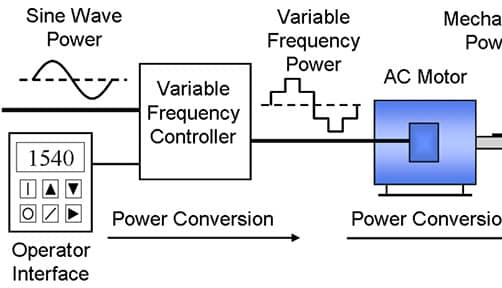
Variable Frequency Drives describe equipment used to control the speed of machinery. Many industrial processes such as assembly lines must operate at different speeds for different products. Where process conditions demand adjustment of flow from a pump or fan, varying the speed of the drive may save energy compared with other techniques for flow control. There are two major problems however to account for with VFD’s.
1. When an application requires more current at a reduced speed, that means more heat and less cooling at the lower speeds. Most VFDs have limits to protect the VFD and consequently the motor. Too low a setting and there will be lot of trips. Too high a setting and there may be damage in high ambient temperatures. So cooling should be available at these low speeds.
2. Variable frequency drives come in various NEMA enclosures such a 1, 12, 3R and 4. The heat sinks for the transistors may be internal or external. Those that are internal such as NEMA 1 or many smaller HP units (and some 3R) are usually vented and rely on airflow through the enclosures. Dusty locations can easily clog air filters, where included, or drag dust in on the microprocessor motherboard and power components, creating electronic problems and excess heat on the power components. Conductive dust can short out power and controls. Dust buildup on the fan blades and external heat sinks can cause excess heat and fan failures. Improper selection, application and/or maintenance can result in problems or premature OVERTEMP faults. Installing chassis mount or units inside improperly vented custom enclosures and/or outside locations exposed to sunlight aggravates this problem as well.
One solution to address these conditions are compressed air operated vortex tube cooling systems such as Panel Coolers made by Nex Flow Air Products Corp. These cooling systems require any open vents to be blocked preventing dirt and dust from entering the control panel. Vortex tube operated coolers also keep the panels are a slight positive pressure to keep out dirt and even moisture in high humidity environments. Vortex tube operated control panel coolers can be provided with a solenoid and thermostat to turn the compressed air supply on and off when needed to provide the cooling only when needed, such as at startup when speeds are normally lower and heat generated higher. Since the cooling is not required at the higher speeds the units can then be turned off automatically (on-off control). A bypass line across the solenoid valve can keep a tiny flow of compressed air into the control panel to keep it clean in a very dirty factory environment. Overall use of compressed air can actually be quite low so energy use is kept minimal. Other advantages with vortex tube coolers is virtually zero maintenance, their ruggedness and the fact they do not produce condensate which has to be taken care with standard air conditioning systems.