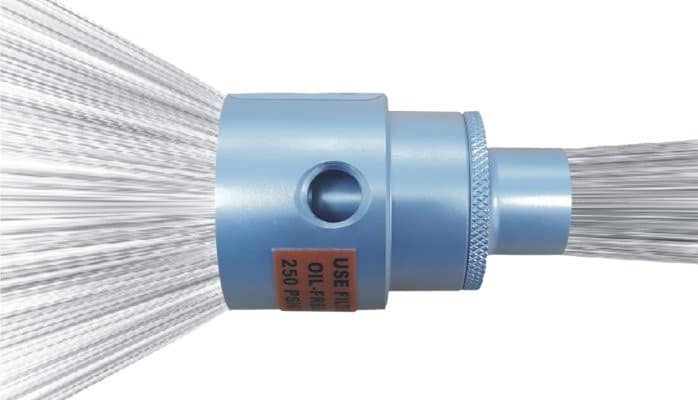
In some industrial casting and forging situations the items made need to be cooled quickly for handling purposes or for an on-going process such as marking or assembly, otherwise the processes cannot be completed properly or handling would not be safe or possible. Cooling can be done with fans but they can be too slow to cool. Similarly using water to cooler involves an extra step of drying, slowing the operation. So the next step would be the use of purely compressed air.
Compressed can be costly to use. Sometimes air nozzles are used and work well for small parts and surfaces but larger surfaces would be very inefficient and use a great deal of energy. In those cases the use of “larger” air amplifiers or air movers is the most efficient solution. They will cool much faster than fans (10% faster or more) which can provide tremendous production cost savings. Air amplifiers convert pressure to flow, minimizing energy losses and also lowering noise levels, a further improvement to the factory environment. Such larger air amplifiers are more efficient in energy use than smaller nozzles. The best sizes for cooling larger parts would be air amplifiers of 1-1/4″ to 2″ in opening size. Cooling a part 6 square inches in area for example would only require four units at relatively low cost in both product cost and energy use, reducing energy well over 50% compared to open compressed air by itself and even savings against smaller nozzles of up to 25%.
Apart from such production applications air amplifiers. in particular sizes in 2″, 4″ and 8″ are used in pulp and paper mills, mines, and even in foundries for cooling personnel due to their portability, and also used for venting as they move a large volume of air.