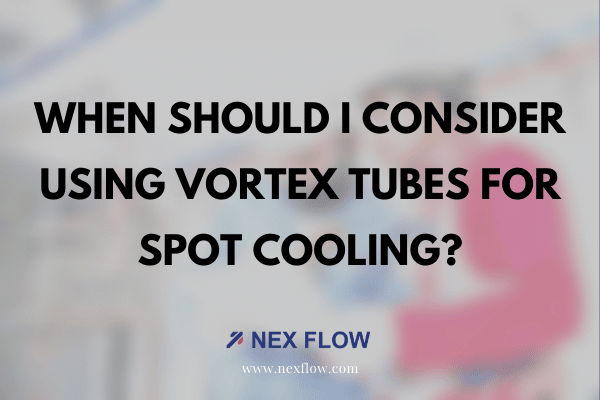
When Should I Consider Using Vortex Tubes for Spot Cooling?
Vortex tubes create a stream of cold air from compressed air. When discussing spot cooling we want to specify that it is a “small spot”, and not a large area such as would be addressed by a big fan for example. We want to focus on a small area from a tiny “spot” to a few square inches, or to an enclosure which can be much larger to a maximum of around 10 square meters, although there are exceptions.
Such “spot cooling” is needed when heat at that spot is either causing a problem in production or, if production can be improved by cooling. The most common “enclosure cooling” is the cooling of electrical and electronic control cabinets that have potential overheating issues and/or where there are dirt problems due to an unfriendly factory atmosphere inside the enclosure negatively affecting performance and potentially the life of the electrical equipment.
One major “spot cooling” application is the cooling of cutting tools during cutting, drilling, or routing process. Traditionally cutting fluid is used in machining but there is a slow but steady movement to “dry” or “near dry” machining because of the increased safety and especially environmental concerns involved with cutting fluids. Cutting fluids need to be properly disposed of, so there are costs of not only buying the fluid but also the disposal of the fluid. One of the reasons progress is somewhat slow in adapting to dry machining is that cutting fluid not only cools, but also lubricates and cleans the machine tool as it operates. This is where mist cooling systems can come in handy because it is not completely dry allowing lubrication but limits the need for cutting fluid. That being said, dry machining is actually necessary for some materials such as glass, plastic, ceramic and titanium. Vortex Tubes produce the cold air which is blown onto the cutting tool to keep heat down and actually produce a better cut and speed up the machining operation. Often these vortex tubes are packaged with an easy to mount system such as the Nex Flow Tool Cooler.
In some machining application, as when a hole must be drilled deep into a part, some lubrication is required. Nex Flow developed the patented Mist Cooler to provide the necessary lubrication by misting lubricant “cooled” by the vortex tube.
There are of course many other systems developed and being developed to spot cool for machining and eliminate coolant using inert gas for example but the vortex tube is also an integral part in many of developments because they only use “air” and cost in comparison is usually much lower. Cooling gas samples in gas analyzers is another good application for vortex tubes. Industrial camera and all sorts of sensors are used in production more and more, and many of these devices are in very hot areas on a production line. Vortex tubes are compact enough to be used to cool these products and keep them functioning effectively and with no maintenance compared to any other alternative.
Other spot cooling applications addressed by vortex tube technology are numerous and limited only by imagination. Some applications for vortex tubes include cooling the nip roll in a plastic converting process for example to prevent sticking, cooling the head of lasers to prevent heat buildup, setting hot melt adhesives so the glue dries faster and to maximize throughput.
Alternatives in such applications can be much larger in size but vortex tubes are very small. Larger size also typically translates into larger capital cost. As vortex tubes have no moving parts, their maintenance is virtually zero and as long as the compressed air is filtered, their life is as long, or even longer than the equipment they are used with. Compact, zero maintenance and low cost are the key advantages of using vortex tubes for spot cooling over other alternatives.
Utilizing vortex tube technology for cooling enclosures is another major application. There are many ways to cool electronic enclosures and other enclosures with traditional air conditioners. However, factory environments can range from quite benevolent to very harsh. A carbon producing facility will be very dusty. This dust can easily get into control cabinets and cause havoc to the electrical components inside. The limitation on the use of vortex tubes is the amount of compressed air available in any facility. The cost is also a major consideration as compressed air is costly. Where vortex tube based products such as the Nex Flow Panel Cooler become an advantage is when the increased energy cost offsets the cost savings in equipment maintenance costs in both material and time, and in offsetting damage to the controls. It is for very hot, humid or harsh factory environments, that increased energy cost of vortex tube cooling systems can be offset by the savings in maintenance time, materials, disposal of filters and improved control life because they keep out the nasty environment from the cabinet enclosures.
Vortex tube controlled cabinet coolers, like the Nex Flow Panel Cooler, have proper electrical certification to assure that no moisture can enter the cabinet. For example, the Nex Flow Panel Cooler models are available to mount onto cabinets with NEMA 12 (IP 54), NEMA 3R (IP 14) and NEMA 4X (IP 66) classifications.
Vortex tubes for these small “spot” and such “enclosure” applications are both a cost-effective and simple solution where cooling is required.