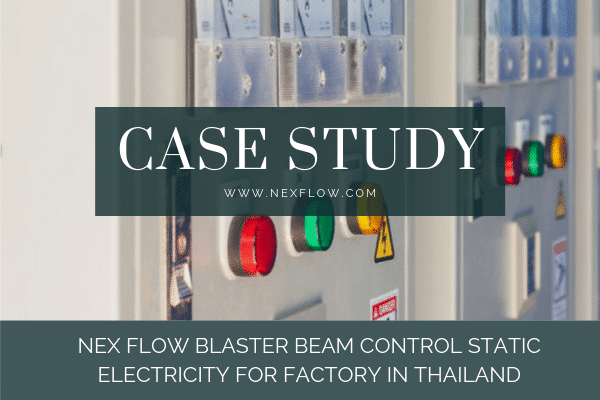
Static can be a major problem in manufacturing processes involving plastic. When producing, cutting or plastic materials and other types of insulating materials, static charge can build up. Even metals and conductive materials can have issues with dust and dirt (normally insulating materials). The issue is often because when these material has static charges, particulates like dirt will adhere to the surface of the object and become very difficult to remove.
One area of expertise for Nex Flow is the cleaning of material that may be statically charged or having to address dirt issues. Our product was recruited by a factory in Thailand for a very interesting application with plastic pipes. Despite the fact that South East Asia is a rather hot and often humid environment for much of the year, static can still build up and cause issues.
With the plastic pipe, the pipe is extruded and then cut. After cutting – small pieces of plastic waste generated from the cut “stick” to the inner walls of the pipe. The plastic cuttings stick primarily due to static charge and is therefore difficult to remove. At the time, our client was using an normal air gun which was tedious and time consuming to remove plastic scraps. Often the scraps were blown further into the pipe making it even more difficult to remove. Yet the pipe had to be cleaned on the inside prior to shipping.
Initially a Nex Flow 6” X-Stream Air Blade Ionizer – a 6” air knife attached to a static bar. This test was performed manually simply by holding the Air Blade Ionizer at one end of the pipe and blowing into the pipe towards the opposite end where the debris had built up. When the air flow from the unit was blown into one end of the pipe, despite the overall length being extremely long (several meters) the laminar flow exiting the air knife “hugged” the inside of the pipe and carried the “ionized” air flow till the opposite end where the particulate was stuck. The static eliminator bar instantly neutralized the static on the scrap that was stuck to the pipe and literally blew every single piece out that was in the path of the wide sweeping air flow. It was actually quite dramatic. The air flow covered over 50% of the inside of the pipe surface. The inside surface of the pipe is relatively smooth so the debris was not sticking due to any no other reason except static.
So while it worked in a manual test, the next step was to find a way to have this done in the production line automatically and to also have the “ionized air” cover the entire surface of the inside diameter of the piping. To meet both requirement, the Nex Flow Ion Blaster Beam was used. The device consists of a Nex Flow Model FX20 Air Amplifier that has a plastic attachment at the outlet end where “amplified” air flow exits. On this plastic attachment is an Ionizing Pin which makes an “ion cloud” that makes the air flow anti-static. This cloud of ionized air then exists the plastic attachment. The plastic is necessary because if the Pin was surrounded by metal, it will draw away too many ions through grounding, thereby weakening the ion cloud and reducing the overall effectiveness of static elimination by the time the air hits the debris at the opposite end of the pipe. The outlet air flow from the Ion Blaster Beam is conical. Just like the air knife, the air flow is laminar. Therefore when the conical air flow is blown into one end of the pipe, the flow profile of the existing air spreads and covers the entire inside diameter, then “hugs” the inside diameter covering the entire inside surface of the pipe, and continues to the end of the pipe with the plastic dust and dirt and all easily blown. The result is a pipe with the inner surface fully cleaned.
At this point one industry myth that needs to be addressed is often claims that an air knife or air amplifier can always eliminate static at distances like 20 feet (6 meters) instantly. It does not happen that way. As the ions, a mixture of positive and negative charges, travel with the air flow, some will recombine along the way. The weaker this “mixture” is, the more time it will take to reduce or eliminate static charges. If the static charge is high, or the target for removal of static is fast moving, a strong ionizing bar or pin would be needed. Nex Flow has stronger static technology available for such situations. The plastic attachment used in the Ion Blaster Beam, as well as a powerful ionizing pin, results in the speed of static elimination to be up to 30% faster than an air amplifier system that uses a metal attachment. This is significant in high speed or highly static applications. Learn more about static elimination here!
FEATURED PRODUCTS
The Nex Flow Ion Blaster Beam comes with, so it can be easily mounted on the customer’s pipe processing machine. As the pipe is cut, it rolls in front of the Ion Blaster Beam, which is placed at the end of the pipe. Then the unit is turned on for a few seconds cleaning out the inside of the pipe. Regardless of which end it is placed, the air flow is powerful enough to remove all debris. The force can also be controlled with a pressure regulator. If the unit, for whatever reason requires more force, the air amplifier that comprises the Ion Blaster Beam has a gap controlled by a shim that can be opened to add more shims. Compressed air is conserved because it is only used for a short blast in every cleaning cycle. Overall very little energy is needed. After the cleaning blast, the pipe is rolled out of the way and a new one replaces it then the cleaning cycle repeats.
The Ion Blaster Beam was a very simple solution to eliminated the time needed to manually clean the pipes along with significantly improving the quality. It was easily installed and requires little maintenance (occasional cleaning of the ion pin), and was able to assure that the compressed air is clean and dry with proper filtration.
Both the Nex Flow Air Blade Ionizer and the Ion Blaster Beam are excellent for cleaning statically charged parts. Not just because they have good ionized air but because of the even coverage of the surface impinged upon by the ionized air. This air knife’s continuous gap (continuous flow) is what you do not get when using perhaps rows of nozzles or drilled pipe and the conical shape of the airflow from the amplifier with an ionizing pin covers a wider area evenly. Unlike what a few small holes can accomplish placed around an ionizing pin. So for class A surfaces in particular like you get in the automotive industry, such applications are much better suited for using air amplification technology along with quality static elimination technology.