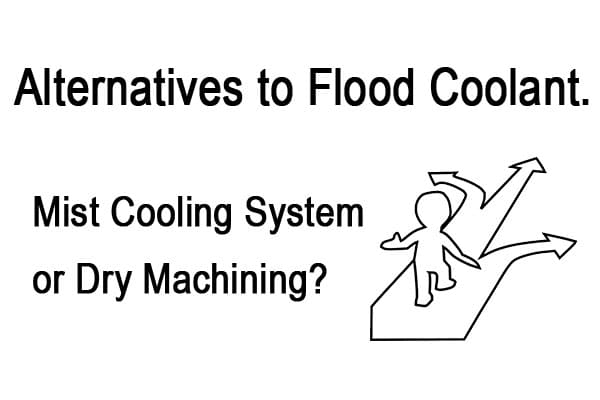
Should I use a Mist Cooling System or go the route of Dry Machining to replace Flood Coolant?
Machine operations still commonly use flood coolant but are working on ways to replace with alternate systems. One such system called Minimum Quantity Lubrication (MQL) attempts to reduce flood cooling. MQL eliminates conventional flood coolant from the machining processes, lubricating cutting tools with a fine spray of oil directed exactly when and where it is needed. MQL reduces oil mist generation; biological contamination of coolant; waste water volume; costs for capital equipment; and regulatory permitting. MQL also improves recycling and transport of coolant contaminated chips. Dry machining is also a growing trend when possible to use and is much less messy than mist cooling systems.
Dry machining has been called the machining of the future and there are many benefits to avoid the use of flood coolant, the most obvious being the increasing environmental considerations and the disposal of waste coolant. (Reference: https://www.theengineer.co.uk/the-benefits-of-dry-machining, Oct 4, 2016). The advantages of cooling, especially to eliminate micro-carbon cracking on carbide tools, are not only for cooling but also to wash out chips from the drilling operations. Machine designs are now taking these things into consideration as the move to dry machining continues, especially as the growth of new composite materials are adopted.
Nex Flow® has developed two products to address dry machining applications – one completely dry and another adapting mist for lubrication.
While obviously using a liquid to cool is easier, compressed air can also be used by adopting vortex tube technology such as that used with our Tool Cooler. A vortex tube takes compressed air and divides the air into a hot and a cold stream – capable of producing very cold temperatures. Normally the temperatures are 0 degrees C. to 5 degrees C. at the exit to avoid condensation. The cold air blows directly onto the desired tool. In many cutting applications this can actually make for a better quality cut. Applications where the vortex tube alone (usually packed in the form of a tool cooler with a mounting magnet to attach to the machine) complete with a flexible hose to deliver the cold air produced, is ideal for cutting, drilling, milling, routing of plastics, glass, and ceramics. Titanium steel is another good application for this totally dry cooling system.
In many situations however, some lubrication is required – for example in deep hole drilling. Without some form of lubrication, the drill can bind. For this purpose, when attempting to eliminate flood cooling, mist cooling has been used where a “mist” is sprayed onto the cutting operation. Nex Flow® has developed a patented system to utilize a vortex tube to cool a lubricating mist which is syphoned up into the unit using a special nozzle. This is their Frigid-X® Sub-Zero Vortex® Mist Cooling System.
As the lubricant is syphoned up, the cold air from the vortex tube cools the lubricant to about 5 degrees C. Then the cooled lubricant is misted onto the cutting tool with volume controllable by an adjusting knob. The liquid being cooled reduces the amount of lubricant needed significantly, up to 20% less than what would be needed with a standard mist coolant. This reduces the environmental effect dramatically, reduces lubricant cost and cools the operation significantly.
The compressed air required for purely dry machining using vortex tube technology is about double that required for using some liquid along with the vortex tube. In both situations it is important that the compressed air is properly filtered to keep the system clean and dry to prevent condensation and any oil clogging up the vortex tube component. Recommendation for filters is a minimum 10 micron water removal filter and if there is oil in the air line, a 0.3 micron oil removing filter. Without proper filtration the systems can be damaged over time and lose effectiveness.
There was a very interesting application recently on board an oil rig where either a Tool Cooler or a Sub-Zero Vortex® Mist Cooler could be used for a particular cutting application. The restriction was that the temperature produced by cutting metal was to be kept under 200 degrees C. due to the nature of the explosion proof rated environment. This could be accomplished by using either system. Lubrication was not an issue so water was used in the Mist Cooler in lieu of any lubricant. In addition, the use of water itself was not an issue for the materials being machined. Both systems were tested.
Both the systems were highly successful in achieving the goal of maintaining any temperature from the operation below 200 degree C limit. In the end, the Mist Cooler was used because of limited compressed air available for the multiple number of systems required.
In most situations, when moving away from flood coolant it comes down primarily to the need for any lubrication in the process. If no lubrication is required, for both reasons of eliminating lubricant cost and a cleaner environment in the workplace, it would be best to use purely dry machining process. However, for dry machining system with multiple stations, care should be taken to ensure adequate amount of compressed air capacity when using a system like the Tool Cooler. MQL systems are certainly an ideal goal to reduce flood cooling when lubrication is also necessary. When using the vortex tube operated mist system the lubricant should be water based and after use, be thoroughly flushed from the system to keep it clear and clean for the next use. Misting however does effect the nearby environment so reducing the amount of liquid is always a plus. Systems like the our mist cooling system can reduce lubricant use (and cost) up to 20% by cooling the mist as it is being used.
Regardless of which system is chosen, anything to reduce and replace flood cooling offer benefits to both the owners and employees of any company both in cost and environmental impact.