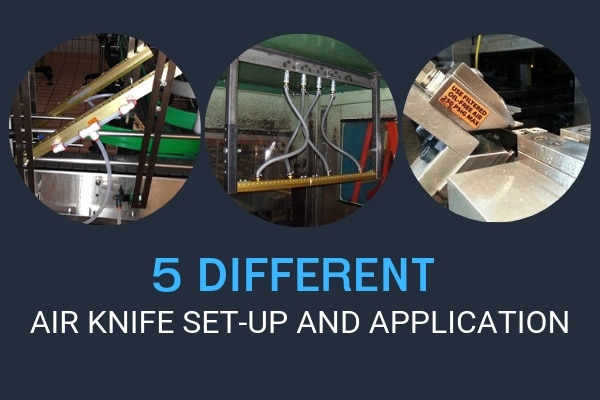
Air knives can be compressed air operated or blower operated and different factors determine which is optimal to use. This article will be focused on the different ways you can set up a compressed air operated air knife. Compressed air operated air knives are used primarily for drying, cleaning, and cooling and also for coating control and drying. There are multiple ways to set-up an air knife system depending on the application.
Below is a list of five common application and the basic suitable set-up
- Drying or removing liquids from the surface of parts
- Debris blow off from parts with special focus on how to remove static electricity from plastic parts that need to be cleaned
- Coating control on parts when a coating is applied and needs to be spread evenly over the part
- Drying or setting of a coating once applied to the part
- Cooling of materials
Drying or Removing Liquids
Compressed air operated air knives are excellent for drying applications especially when drying relatively smooth and flat surfaces because of the high shear force. Blower operated systems often rely on heat as well as large blower mass flow to remove liquid but this can often leave stains on the surfaces left over from chemical residue. Compressed air operated units will have the added energy to remove all the liquid minimizing any possibility of stains. In addition, you need much less of a footprint to dry in any conveyed system as any liquid droplets left after drying are so small they evaporate very quickly. In these applications the air knife flow is directed against the direction of the moving product about 3 degrees in slow moving situations and incrementally increased to as much as 30 degrees for fast moving applications. The actual pressure used depends on speed and viscosity of the fluid removed and the roughness of the surface where the liquid is deposited. The greater the speed, viscosity and roughness, the more pressure is needed. Input air pressure can range anywhere from 60 to 80 PSIG.
Debris Blow Off
Compressed air operated air knives are also ideal in blowing off relatively light debris as compared to blower systems for the same reason as when dying, ie: light scrap off conveyors, dust and debris. The same rules apply regarding the angle of the air knife as with drying and is again directed against the direction of the moving target. It can be 3 to 30 degrees depending on speed but also depending on the nature of the material being blown off. For dust blow-off – it can be treated like liquid. For larger material or clumps of product, the angle can vary widely and needs to be tested for best effect in cleaning. Pressure however can often be very low (as low as 30 PSIG for light dust and debris) but of course can ramp up to 80 PSIG for heavier material. For very heavy material, the air gap of the air knife can be opened up for more force and power but that will also increase the amount of compressed air needed. For particulate or objects that need to be removed but only show up intermittently, a sensor system can be set up to detect the material and turn on the air supply only when needed to conserve energy as compressed air operated air knives can be instant on and off in operation. When having to clean particulate for statically charged surfaces such as plastics or film, an ionizing bar (static eliminator) can be attached to the air knife. When used in conjunction – unless the particulate is also very sticky – pressure as low as 30 PSIG and even less is capable of de-dusting a statically charged surface. Learn more about how a static eliminator works.
An example of such an air knife with a static bar is the Air Blade Ionizer. If noise is a concern a Silent X-stream® model is also available. For very high charges or fast moving target, a stronger static bar may be used as with the our Triple X Air Blade Ionizer.
Coating Control
A compressed air knife with a very sharp edge air flow such as the X-Stream Air Blade® are ideal for use in controlling the level of coating applied to a product. The sharp, even and targeted flow from this unit can control the amount of coating on a product as the coating is first applied, then spread with the help of the air knife. The required pressure depends on speed and the depth required for the coating but easily controlled with a regulator and can vary widely depending on the viscosity of the costing as well. In coating control the laminar flow produced is important and gives much better control than the more turbulent flows produced by blower operated systems. In coating control the angle of the air knife is usually around 3 to 5 degrees due to the slower speeds involved.
Drying or setting of a Coating
Ever wonder why compressed air gets cold? There is a slight cooling effect when air leaves a compressed air operated air knife as the air goes from high pressure to low pressure. Air flow is amplified as atmospheric air is entrained along with the compressed air but there is still a slight cooling effect. This cooling effect assist in helping to dry or set a coating once applied to the product to ensure an even finish. Pressure used is typically quite low at 20 to 30 PSIG and angle around 3 degrees against the flow of material.
Cooling of Material
As mentioned above, there is a slight cooling effect which helps when used to cool materials. But in addition to the cooling effect, the laminar flow and high velocity of the air produced by a compressed air operated air knife can “cut” through the boundary layer produced by heat generated in a hot target and help cool the material. The cooling occurs due to the wind chill effect. How fast the material can be cooled depends on several factors. The higher the initial temperature, the faster it will cool, and the rate of cooling will slow logarithmically as the material gets cooler. Dwell time is also important. It is no question that you need time to cool an object. So when cooling with an air knife the product should travel slowly. Alternatively you can use several air knives, one after the other, to have enough exposure or dwell time to blow on the product and cool. The angle of the set-up should again be about 3 degrees with pressure typically at 80 PSIG to get the optimum mass flow and velocity for cooling.
So whether drying, cleaning, controlling coating, setting a coating or cooling, compressed air operated air knives offer an economical and viable solution. To further reduce your compressed air energy consumption – don’t forget to check out this article!