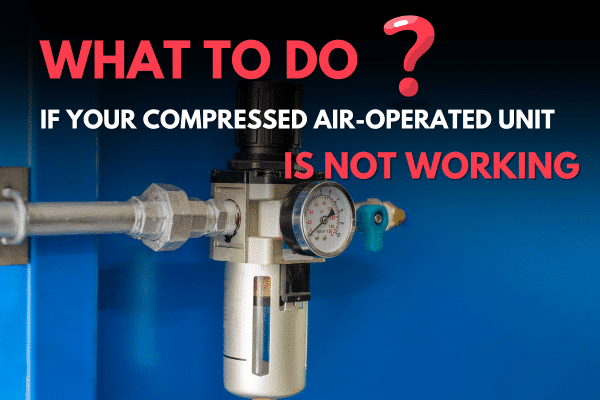
Compressed Air Operated unit not working? Many customer calls we receive have connected long air knives, high-capacity vortex tubes, Panel Coolers, or other products. These are known to be high consumers of compressed air. As a valued user of these products, your role in maintaining them is crucial. It’s essential to be aware of potential issues and how to address them.
Compressed air is an invisible power source and relatively safe (no electric shocks or leaks are seen). Although not noticed as much as other power sources, this safety aspect should reassure you about its use and help you handle it confidently. Your experience with compressed air, whether it’s hooking it up to a machine, air gun, nozzle, or other device, is a testament to this safety.
One aspect often overlooked is how the compressed air is fed to the air-consuming product.
The device using the compressed air will automatically try to use the flow for which it is designed. However, if that flow is unavailable due to a lower supply, loss through leaks, or a pressure drop in delivery, the compressed air supply will compensate by dropping pressure. Understanding this can empower you to identify and address potential issues with your compressed air-operated unit.
The performance of any compressed air-operated product, whether it is an air nozzle, air for amplifier, vortex tube, or even an air-operated conveyor, is determined by flow but also by pressure. If performance does not seem to be there, the first thing to check is the pressure.
Install a pressure gauge slightly upstream from the device using compressed air. While the device is operating, measure the pressure. If the pressure is where you want it (usually around 80 psig), then the problem is unlikely to be a lack of adequate flow.
But, if the pressure is less and falling, there are two more things to check.
The first is if there is adequate compressed air supply. You need to check that you have enough compressor power available and also check the other areas using the compressed air. This can be a simple, quick physical audit or record check.
However, people usually check available power before purchasing the product by consuming the compressed air. More often than not, a pressure issue arises from using an air supply line that is too long and too small in diameter for the application.
However, before purchasing the product, consumers usually check the available power by using the compressed air. Often, a pressure issue arises from using an air supply line that is too long and too small in diameter for the application.This causes access pressure loss. While it may be as much as 90 PSIG at the beginning of the air supply line, access pressure loss may have dropped the pressure as much as 30 PSIG by the time it reaches the air-consuming device.
Small air nozzles, short air knives, and low-capacity Panel Coolers or vortex tubes rarely experience this issue because the air supply lines are generally adequate. However, people do not always consider it because the problem only occurs with high-usage products.
Most compressed air applications in a factory work well with customary hose and pipe lengths and diameters, but people can forget this aspect.
However, being aware of compressed air’s sensitivity to pressure drop can increase awareness in other areas. Addressing such losses can improve efficiencies and save energy.
An online consultant project used some venturi devices. The client was seeking to potentially change the devices to more efficient ones. The situation was analyzed. There was no benefit to changing the existing devices, as they were already efficient in their design and were in an ideal application. The change was to use much larger connecting airline diameters to reduce pressure drop. It solved the problem.
Compressed air auditing focuses primarily on air compressor operation and air leaks, which are both valid aspects. But one of the cheapest ways to save energy and improve efficiency is often upsizing the airlines.
Nex Flow’s low-cost online consultancy helps discover, explain, and assist in addressing compressed air point-of-use issues.