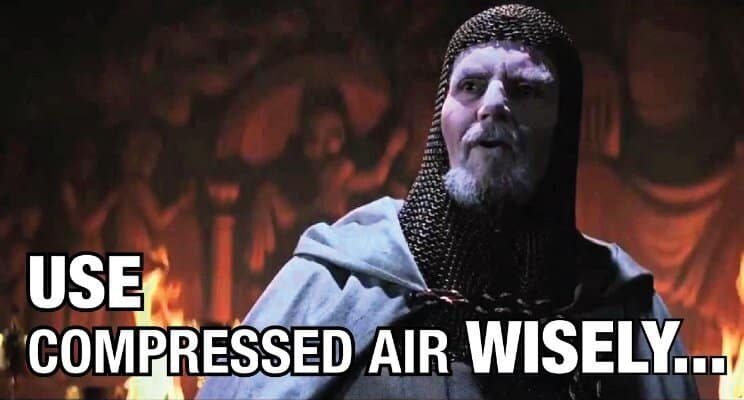
Possible areas to address in a compressed air system to save energy are listed below. Some, or all may apply to your system:
- Piping Design, redesign: Increase the diameter of the piping; reduce the length of the network; loop the network; limit elbows and bends. Check for and repair leaks regularly.
- Install a system with several pressure values (multi-pressure systems or networks), either separate or connected to each other determined by what is required by the compressed air consuming equipment or application. Reducing 1 atmosphere (14.7 PSI) or bar pressure provides an energy saving of 8%.
- Utilize the heat of compression: 90 % of the electrical energy consumed by a compressor is converted to heat. In practice, 60% of this heat can be recovered and used within a factory operation.
- Consider automatic control of the compressed air production via a variable speed compressor or an automatic control of all the compressors according to need. Average 15 % savings with automatic control (from 5 to 35 %). Not all systems will benefit but a compressor supplier can assist in evaluating what is appropriate for your plant.
- Reduce the air inlet temperature to the compressor: 1% consumption savings are obtained every 3 degree C reduction. Check from where the air intake draws into the compressor(s).
- Replace compressors with new and better machine(s) with lower specific energy consumption (more compression stages) that may be more suitable to the requirements of your system.
- Use “leak-loss free” condensate traps. A high-performance network allows for a maximum pressure loss of 7 PSI or 0.5 bar throughout the line.
- Enhance and check pressure regulating valves, filters, lubricators, driers and condensate traps for quality products that minimize pressure drop and leaks.
- Dry off and filter air moderately as needed abut not more. Too long a drying or too fine in filtering leads to unnecessary overconsumption of energy as much as 6%.
- Monitor compressed air use at key points.
- Design proper storage capacities to allow operation with higher output of compressors and to avoid unexpected switching on or off.
- Install control equipment such as flow meters and air meters, current meters, and pressure gauges.
- Replace leak generating equipment parts, cracked air hoses, old sticking connectors and valves, etc.
- Use energy saving, engineered blow off nozzles and air guns, amplifiers and air knives.
- Use sensors and solenoid valves to turn off compressed air to machines when not in use.
- Divide the network into areas with pressure controls or appropriate isolation valves. Close the network areas when not used.
- Place storage capacities next to machines with high variation in air required.
USE COMPRESSED AIR WISELY!!
Nex Flow Air Products Corp. manufacturers compressed air technology for blow off, drying, cleaning, cooling, and moving and constantly strives to improve their products’ performance and quality and to educate in the optimum use of, and in applications of compressed air.