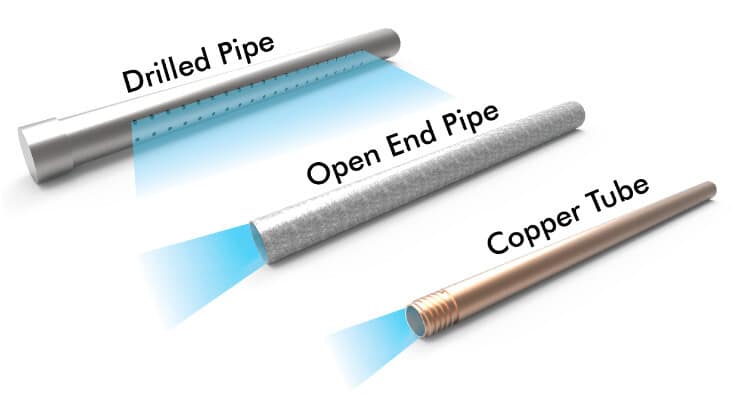
Compressed air is used extensively for blow-off, cooling, and drying applications as blowers are not always powerful enough or have other disadvantages in the specific application. Since compressed air is a costly power source factories should reduce the compressed air cost by utilizing high efficiency engineered nozzles, air amplifiers and air knives. This technology is designed in such a way that it uses the compressed air to entraine and accelerate the surrounding air to deliver the same mass transfer effect as the single large opening in a standard nozzle, and even proving a better and more effective force because it reduces turbulence by providing laminar flow over a greater distance. The side effect is not only much less energy use, but also dramatically reduced noise levels.
However it is still very prevalent in factories to just use open tube and pipe for blowing compressed air. Even a small tube can exhaust a great deal of air wasting energy. The amount of air can be determined with a mathematical formula A more extensive formula is dependent on temperature and the condition of the inlet air, but by assuming standard conditions we can use the following simplified equation:
14.485 x D2 x (psig + 14.7) = “X” SCFM
Where:
- D is the inside diameter of the opening in the pipe or tube in inches
- PSIG is the compressed air gauge pressure in pounds per square inch
- SCFM is the resulting flow rate in standard cubic feet per minute
Let’s assume we have just a small copper tube with an opening of 1/8 of an inch, not an uncommon site in blow off operations with compressed air at 80 PSIG. Using the formula it will consume:
14.485 x (.125)2 x (80 psig + 14.7) = 21.43 SCFM